By Lyra Fontaine
Wearable electronics, from health and fitness trackers to virtual reality headsets, are part of our everyday lives – but finding ways to continuously power them is a challenge. UW researchers, led by ME Assistant Professor Mohammad Malakooti, have developed an innovative solution to this challenge: a wearable thermoelectric device that converts body heat to electricity.
By printing multifunctional soft matter and embedding inorganic semiconductors, the researchers have created first-of-its-kind thermoelectric generators (TEGs), which are soft and stretchable, yet sturdy and efficient – properties that can be challenging to combine. The research paper about their findings, “Printing Liquid Metal Elastomer Composites for High-Performance Stretchable Thermoelectric Generators,” was recently published in Advanced Energy Materials.
Unlike other flexible thermoelectric devices made of inextensible copper electrodes and carbon-based composites, these TEGs are durable for long-term use and can bend, twist and stretch. They remain fully functional even after more than 15,000 stretching cycles at 30% strain, which reflects the extensibility limitations of skin and therefore is a highly desirable feature for wearable electronics and soft robotics. The device also shows a 6.5 times increase in power density compared to previous stretchable thermoelectric generators.
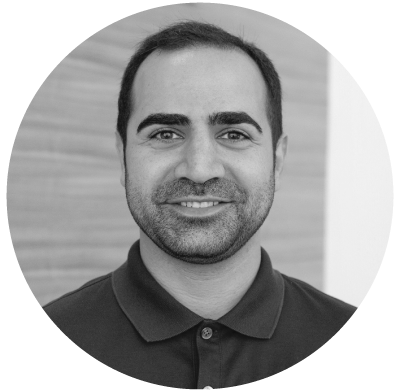
“It’s a 100% gain if we harvest thermal energy that would otherwise be wasted to the surroundings. Because we want to use that energy for self-powered electronics, a higher power density is needed,” says Malakooti, who is part of the Institute for Nano-Engineered Systems (NanoES) research community. “We leverage additive manufacturing to fabricate stretchable electronics, increase their efficiency and enable their seamless integration into wearables while answering fundamental research questions.”
“One unique aspect of our research is that it covers the whole spectrum, all the way from material synthesis to device fabrication and characterization.”— Mohammad Malakooti, ME Assistant Professor
To create the stretchable TEGs, the researchers 3D printed elastomer composites with engineered functional and structural properties at each layer. The researchers integrated functional filler materials – namely liquid metal alloys that provide a high electrical and thermal conductivity – in elastomers to address limitations in earlier elastomer-based thermoelectric generations, such as low stretchability and conformability, inefficient heat transfer and a complex fabrication process. They also embedded hollow microspheres to direct the heat to the semiconductors at the core layer and reduce the weight of the device.
Two layers of highly conductive liquid metal composites are used for heat transfer, and one insulation layer separates the two and encapsulates thermoelectric semiconductors. A different liquid metal elastomer composite with large liquid metal droplets was printed to serve as a stretchable electrical interconnect between the semiconductors.
“Finishing this project took a lot of dedication, and I really enjoyed the journey,” says Youngshang Han, ME master’s student and the lead author of the paper. “I had never been involved in soft matter-based energy harvesting research before, so everything was new to me, and I learned a lot.”
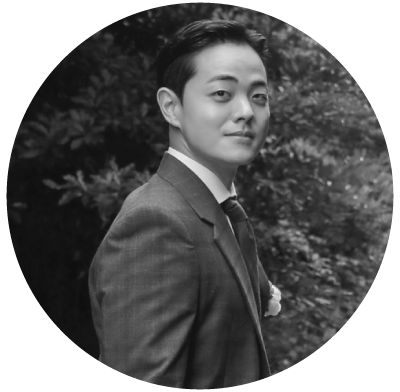
The researchers are excited about the future possibilities and real-life applications of wearable electronics. The new paper demonstrates how TEGs can be printed on stretchable textile fabrics or curved surfaces, showing how their discovery could be applied to clothing and other objects. It was also demonstrated that 3D structured heatsinks – components with a large surface area that help dissipate heat – can be directly printed on thermoelectrics using their novel approach.
“One unique aspect of our research is that it covers the whole spectrum, all the way from material synthesis to device fabrication and characterization,” Malakooti says. “This gives us the freedom to design new materials, engineer every step in the process and be creative.”
Malakooti’s research group iMatter Lab will continue studying soft and stretchable TEGs with the help of a recent research gift from Meta Reality Labs. Han will be joining the group as a Ph.D. student this fall. “I’m thrilled to be part of a fast-growing field and want to continue to push the limits of wearable electronics in future projects,” Han says.
Students and researchers in the iMatter Lab gain a broad range of multidisciplinary hands-on skills, including materials synthesis, electromechanical testing, 3D printing and fabricating electronic devices. Being able to conduct research in-person again has been a rewarding experience.
“It’s been amazing to see students in the lab and to be there for them,” Malakooti says. “They each bring their own unique skills and research interests, such as multiphysics modeling, materials characterization, circuit design and building a test setup.”
Originally published August 8, 2022 on ME department website.